Transforming Fixture Protection See how NanoSlic can help
Conformal Coating Removal from Fixtures
Removing a conformal coating can be costly and time consuming. Conformal coatings can be silicone, acrylic, urethane, epoxy, paralene, and more. Each presents its own challenges for removal. Some will only respond to mechanical methods, while others require a chemical solvent.
In electronic assembly, fixtures are used to secure the PCB to the assembly line machinery while the coating is applied. Whether a platform, tray, or hook, the build-up of overspray to the exposed fixture degrades its usability and must be accounted for in the manufacturing process.
Removal Methods Include:
Don’t just take our word for it:
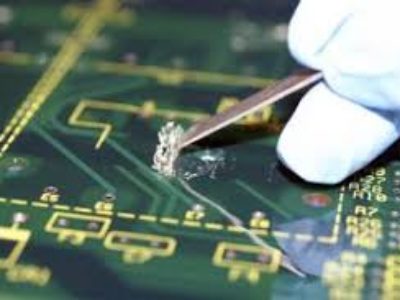
Stop wasting time.
Easy and Hassle-Free Conformal Coating Removal with Nanoslic.
Pre-treating fixtures with NanoSlic’s unique hybrid formula allows for coatings to be removed with a minimum of hassle.
Chemical solvents, microabrasion, laser ablation and mechanical peeling techniques each have significant downsides in conformal coating removal, from damaging components to discolorations and warping to expensive removal equipment.
The key to our proprietary formula is the nanometer-thick hydrophobic and oleophobic outer shell.
It resists adherence to every type of conformal coating currently in use. NanoSlic utilizes a ceramic platform chemistry designed to withstand the harshest environmental. Because it repels both water and oil-based substances, conformal coatings to not stick.
Nanoslic provides an essential layer of protection, smoothly contouring the fixture surface to present an ideal surface for the removal of the overspray coating.