Nanocoatings
What are nanocoatings?
Nanocoatings are ultra-thin layers or chemical structures that are built upon surfaces by a variety of methods. Some nanocoatings are polymers, either polymerized in-situ or prior to application.
Technically, a nanocoating is a coating that’s measured on the nanoscale. Another industry definition is a coating that is no more than 1–100 nanometers thick.
To compare, the typical automotive paint is approximately 125 microns or 125,000 nanometers. At the nanoscale, quantum physics comes into play. Nanocoatings can be structured one molecule thick, or they can be built up from multiple molecular layers. Then these are hybrid nanocoatings, such as NanoSlic, which combine multiple layers of nanocoatings to deliver a wide range of benefits.
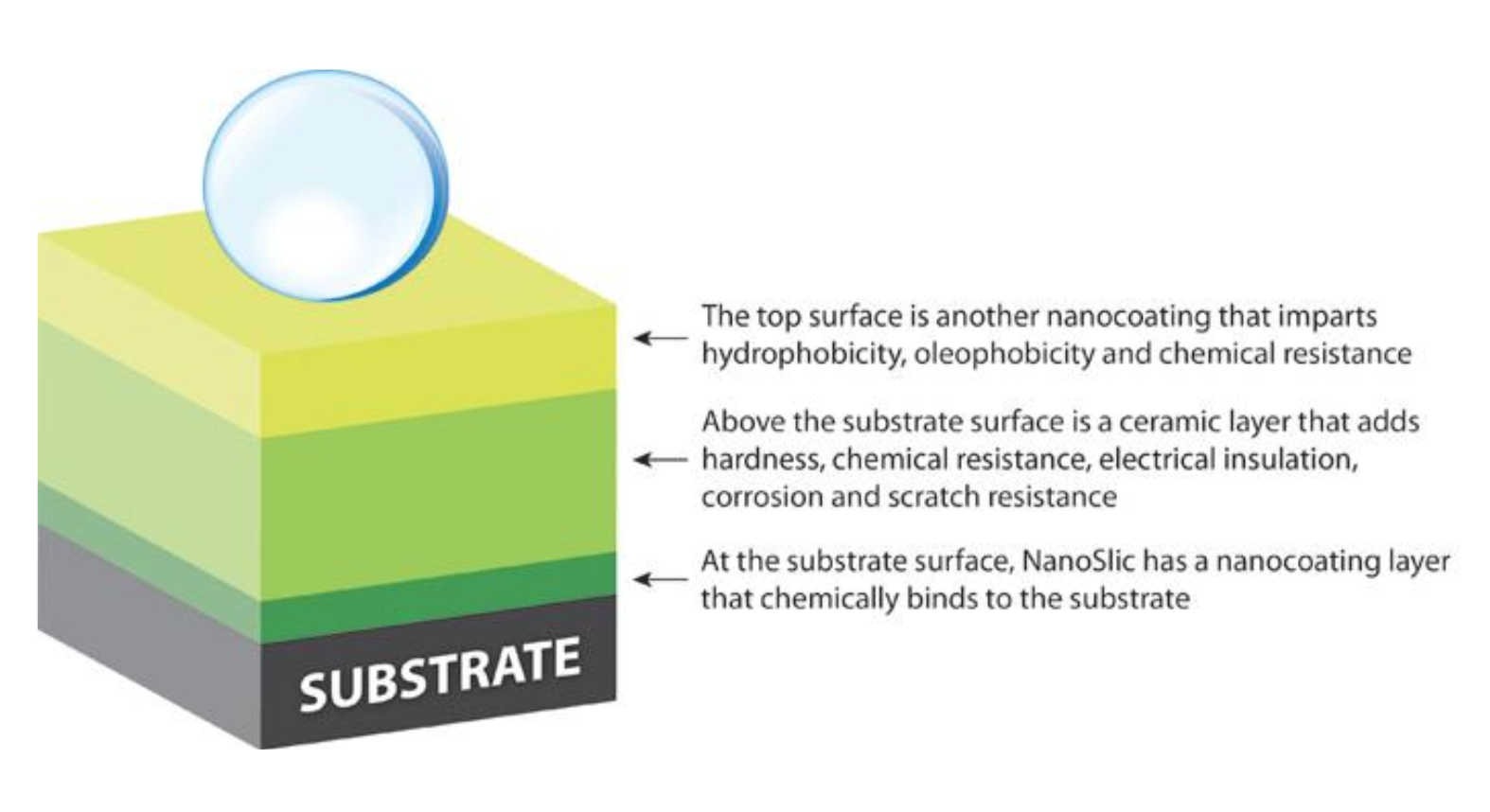
Why work with nanocoatings?
Typically, nanocoatings are used to impart a particular chemical or physical function to a surface. For example, they may impart hydrophobic and oleophobic properties to improve corrosion resistance, enhance insulative or even conductive properties. They can provide self-cleaning properties, as well as resistance to water, static, oil, scratches, bacteria, corrosion, fungus, friction, UV rays, and more.
Nanocoatings emit much lower levels of volatile organic compounds (VOCs) than traditional polymer coatings, which has been driving increased demand. They’re particularly useful in contexts where there are strict VOC limits.
Because nanocoatings are so thin, they’re also transparent to the naked eye. That’s a huge boon to products where aesthetics come into play. They can even be used to extend the life of a product’s color or gloss.
Nanocoatings can be applied to a wide variety of substrates and bond chemically with non-porous surfaces. For example, they work with metals, ceramics, plastics, and polymers. They can even be applied to other nanocoatings.
How are nanocoatings used?
Nanocoatings are used across many industries and fields. That includes electronics, medical equipment, industrial manufacturing, transportation and aerospace. When properly formulated, they can prevent fingerprints from forming on automotive surfaces and prevent harmful bacteria from growing in medical settings to helping clothing repel moisture.
Because they are typically transparent, nanocoatings useful in applications where opacity would be a problem. For example, certain nanocoatings can make windows resistant to heat and UV rays. The window stays clear but gains the additional properties. Today, researchers are using nanocoatings to solve many common problems and challenges. From pharmaceuticals to paints, they’re appearing in a huge variety of applications.
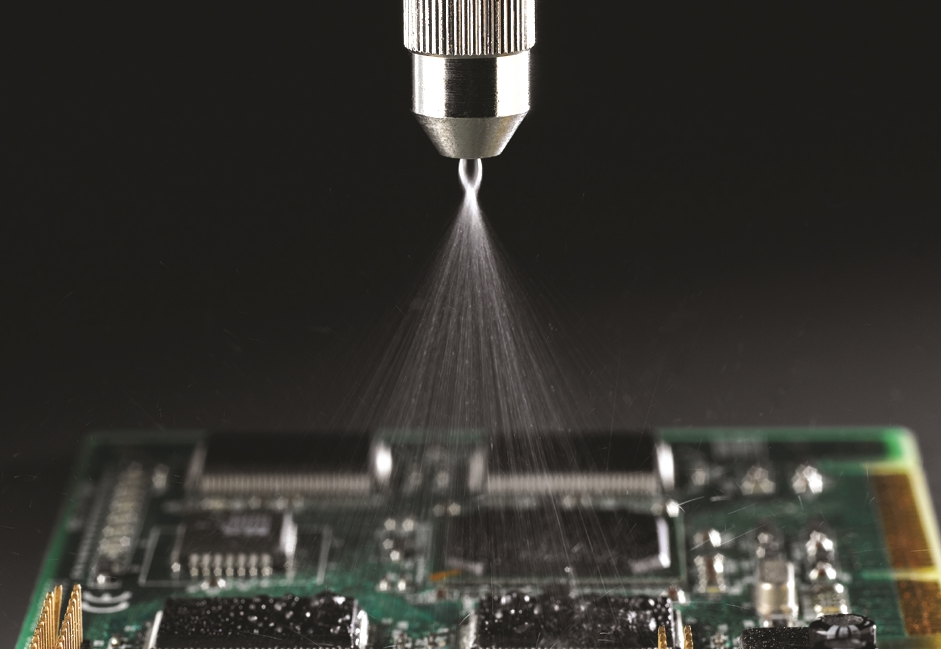
What is NanoSlic nanocoating technology?
NanoSlic offers a variety of hybrid nanocoating products. Our products form a dense network of strong chemical bonds on the substrate; an inert, high-performance binder polymer layer; and a hydrophobic, oleophobic contact surface. They make cleaning easier, protect and enhance surfaces.
How can nanocoatings help me?
Historically, application of nanocoatings has required specialized equipment, complex procedures, and extreme heat. They are often applied with techniques such as chemical vapor deposition or plasma spray. But now, new developments in chemistry and coating technology making nanocoatings much more accessible. NanoSlic products are useful in a wide range of applications, from commercial to industrial, including:
Electronics | Industrial | Aerospace | Automotive | Marine | Medical
Text content