NanoSlic Ceramic Coating Applications
SMT Stencil Coating
The NanoSlic coated stencil is the most advanced solder paste stencil available. Using advanced polymer chemistry, this coating has been developed to address the increasing demands confronting the electronics assembly industry. The coating is applied using a proprietary process which permanently coats both the underside of the stencil and aperture walls. This coating technology is highly hydrophobic and oleophobic, providing superior paste release and allowing more print cycles between cleaning.
The benefits are numerous and include:

Increased paste transfer efficiency

Reduced stencil underside cleaning

Consistent print from board-to-board

Highly robust and durable
Protection
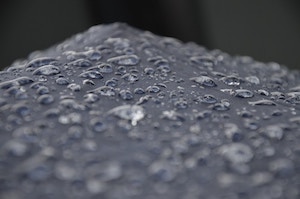
VOC-free NanoSlic is perfect for extreme corrosion, chemical and solvent resistance, water repellency and abrasion protection. It improves part durability and performance through its outstanding hardness, modulus, flexibility, and abrasion resistance.
Improvement
NanoSlic is ideal for enhanced surface hardness, planarity, smoothness and, with tinted grades, a high-performance design alternative.
Our nanocoatings are resistant to a broad spectrum of chemicals, including water-based solutions and most solvents. Water and organic-based materials bead up, roll off and leave the surface clean.
Any application that needs to last longer, be easier to clean, or protected from the environment will benefit from NanoSlic. Industries include:
- Industrial
- Automotive & Marine
- Consumer Goods & Appliances
- Paints & Architectural Coatings
How to Use NanoSlic
While most nanocoatings and ceramic coatings require extremely high temperatures and advanced systems to apply, NanoSlic brings these high-performing protective coatings into an easy-to-use commercial format.
As with any coating, proper surface preparation is critical to achieve superior NanioSlic protection. For bare metallic surfaces, we highly recommend using our NS PreClean solution. Spray the surface with NS 50 and wipe with a lint free wiper. Then let it act for 60 seconds. Spray again and rinse well with distilled or DI water for 60 seconds. Allow the surface to dry in its own or dry the surface with a lint free wiper or use clean, dry air. The surface must be completely dry prior to coating. Ensure no dust, lint, or other contamination remains on the surface prior to application of the coating.
Glass and ceramic surfaces should be cleaned with an alcohol, preferably isopropyl alcohol. Polymers, plastics and coatings, especially those with a glossy surface may need to be lightly abraded prior to application of NanoSlic. NanoSlic coating can be applied through spraying, dip coating or wiping with a lint free cloth – depending on specific application needs. Application should be done in a dust free area. When coating, strive for consistent thickness and streak free layers. NanoSlic will obtain properties in the range of 0.2-4.0 microns dry film.