Oleophobic Coatings
“Oleo”
refers to “oil,” but as commonly used, refers to most organic liquids.
“Phobic”
comes from the Greek root “phobos,” meaning “fear.”
=
“afraid of oil”
is the literal meaning of “oleophobic”
Therefore, the term “oleophobic” commonly refers to a
surface that repels oil and oil-based materials.
When oil and oil-based materials come in contact with an oleophobic surface, individual drops of liquid will bead up and will roll off or slide off the surface with ease.
Like hydrophobic surfaces, larger amounts of organic liquids will pool together, the edges pulling back from the oleophobic surface and move as one sheet. This effect can also be described as de-wetting – where the liquid pulls away and the surface seems to remain totally dry.
With the potential to impart properties such as stay-dry or easy-to-clean, oleophobic coatings and treatments are finding their way into more mainstream applications. Anti-smudge and anti-fingerprint coatings are oleophobic and are used widely on touchscreens.
What makes a surface oleophobic?
Most organic fluids are slightly polar to non-polar, which means an oleophobic surface must be very non-polar. To achieve this condition, a surface must contain non-polar atoms such as silicon, fluorine or chlorine. In many instances, these atoms are formed into polymeric molecules that form a wall of non-polarity at the surface.
It is interesting that some surfaces are hydrophobic but not oleophobic. Meanwhile, some surfaces can be both hydrophobic and oleophobic.
Have questions about oleophobic coatings?
Measuring Oleophobicity:
How can the degree of oleophobicity be measured?
This can be determined by measuring how “spherical” a drop is that is sitting on the oleophobic surface. In hydrophobicity, water is used as the test fluid. However, in oleophobicity, other fluids are used which are typically short-chain alkanes.
One of the most common standard fluids for measurement is n-hexadecane. As the oleophobicity of the surface increases, the surface tension, although comparatively low, causes the liquid to pull itself away from the surface more and more into a sphere.
If a line is drawn tangent to the drop as it contacts the surface, then the angle (θ) between that line and a line parallel with the surface, is said to be the Contact Angle (CA).
Surfaces with an n-hexadecane CA of 60°-80° are considered very oleophobic. An example of historic importance is polytetrafluoroethylene (Teflon,) with a contact angle of 65°. Polytetrafluoroethylene is well known for its repellent, non-stick and non-friction surface.
Oleophobic surfaces do not repel a liquid. There is simply no attraction between the surface and the liquid droplet. If there was an attraction, the surface would be considered oleophilic. Oleophilic means “oil-loving.” Oleophilic surfaces attract oils, or organic fluids, and allows it to level out or wet out. Most surfaces are oleophilic relative to the oily liquid, because of its low surface tension tends to spread out.
Measuring Contact Angle:
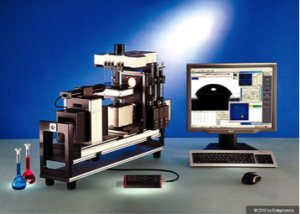
To measure the contact angle, an instrument called a goniometer is used. “Goni” is the Greek prefix for “angle.” This instrument deposits a drop of liquid onto the surface of the substrate and then measures the contact angle using a video camera and specialized software.
More sophisticated equipment and software programs enable the researcher to analyze the surface in different ways. Today, the study of surface chemistry and properties is expanding rapidly.
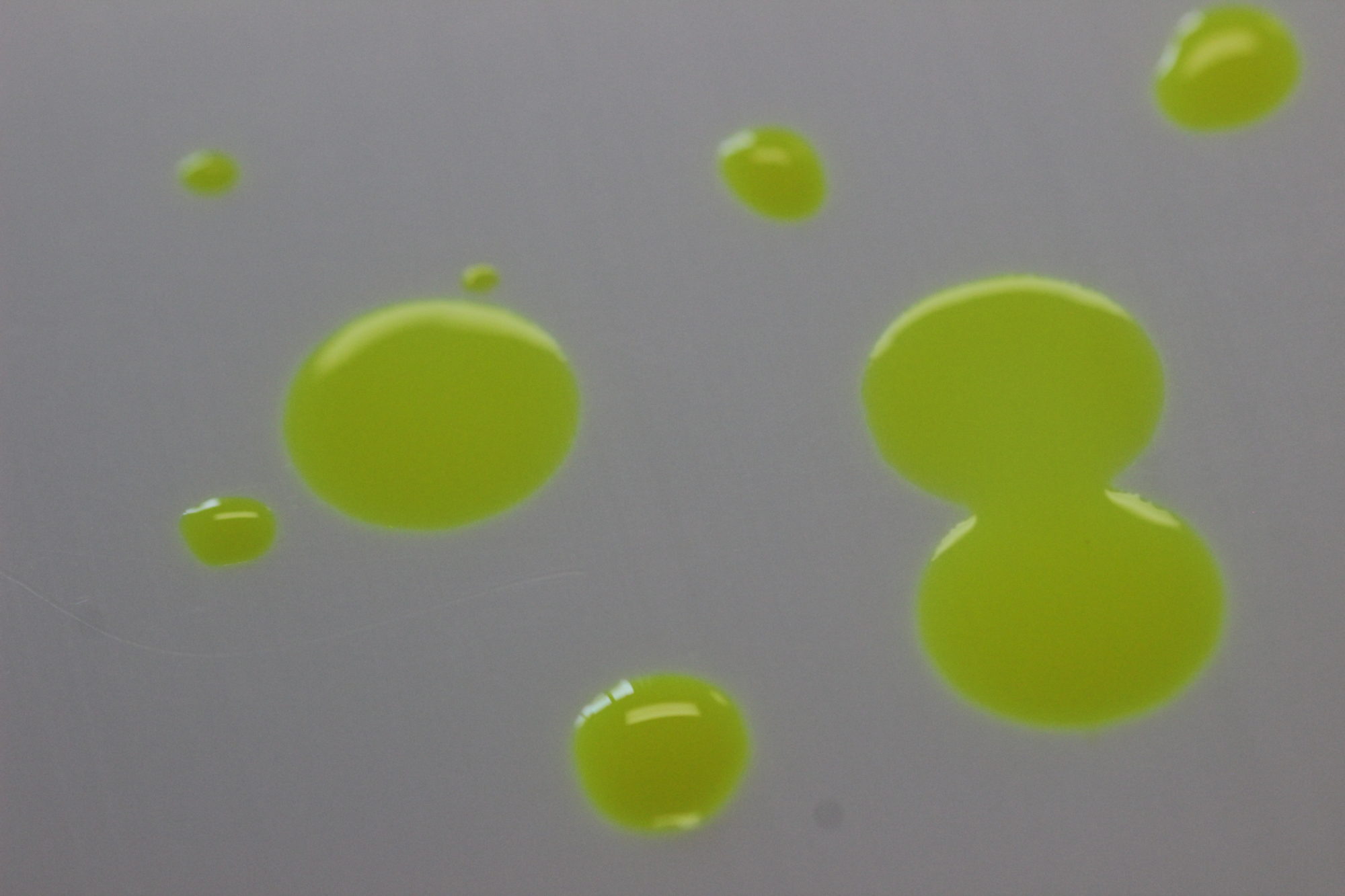
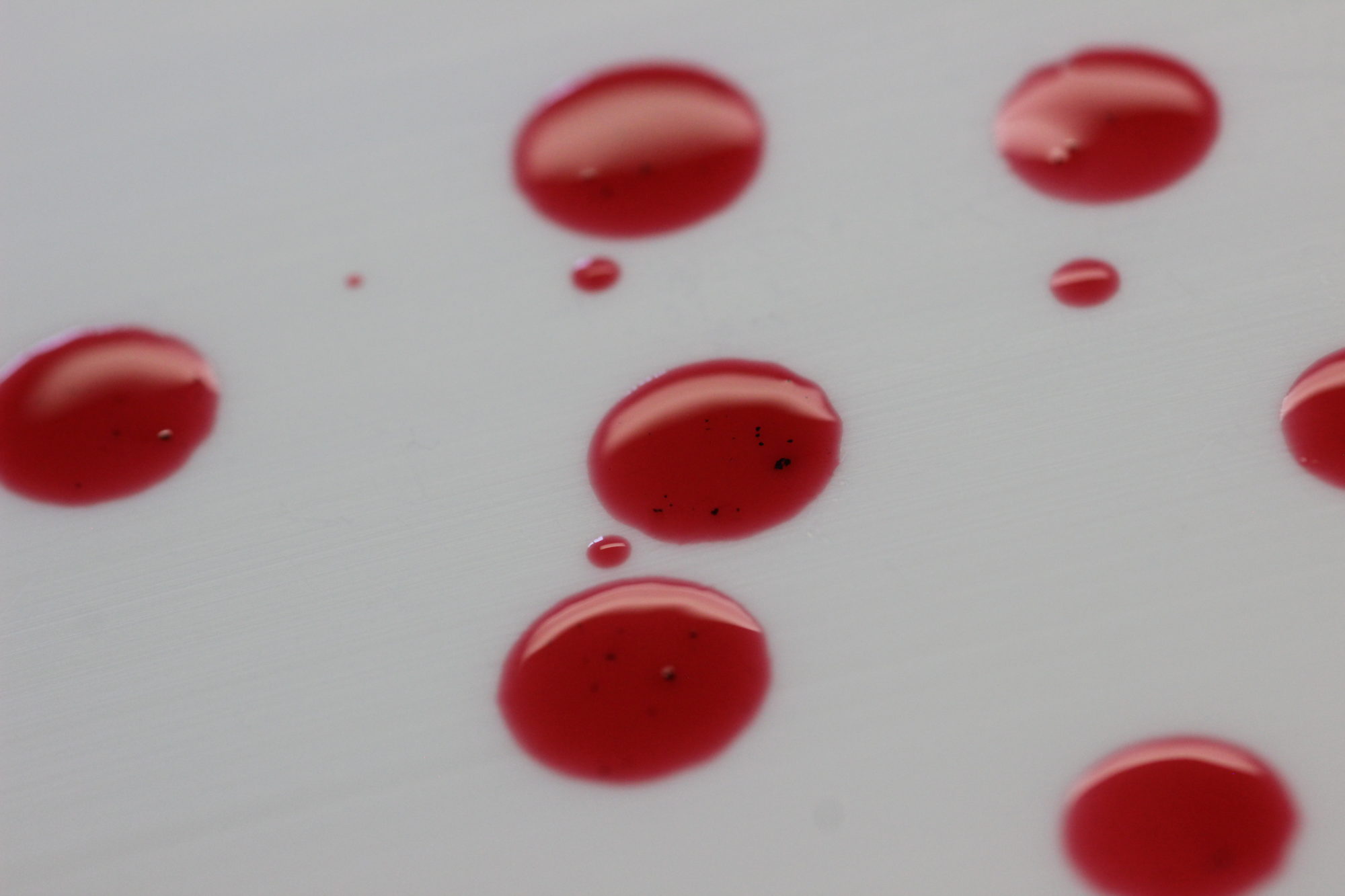
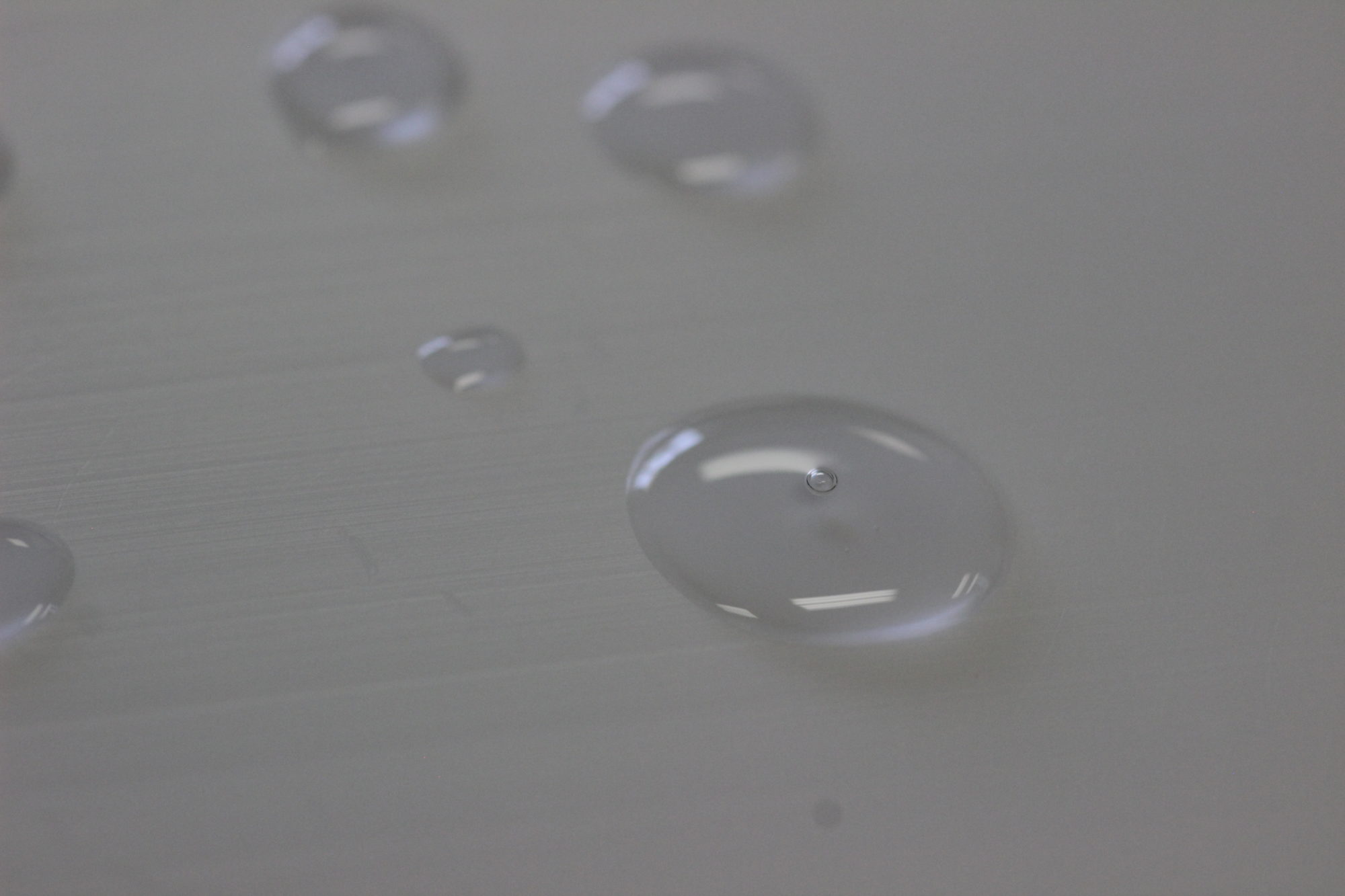
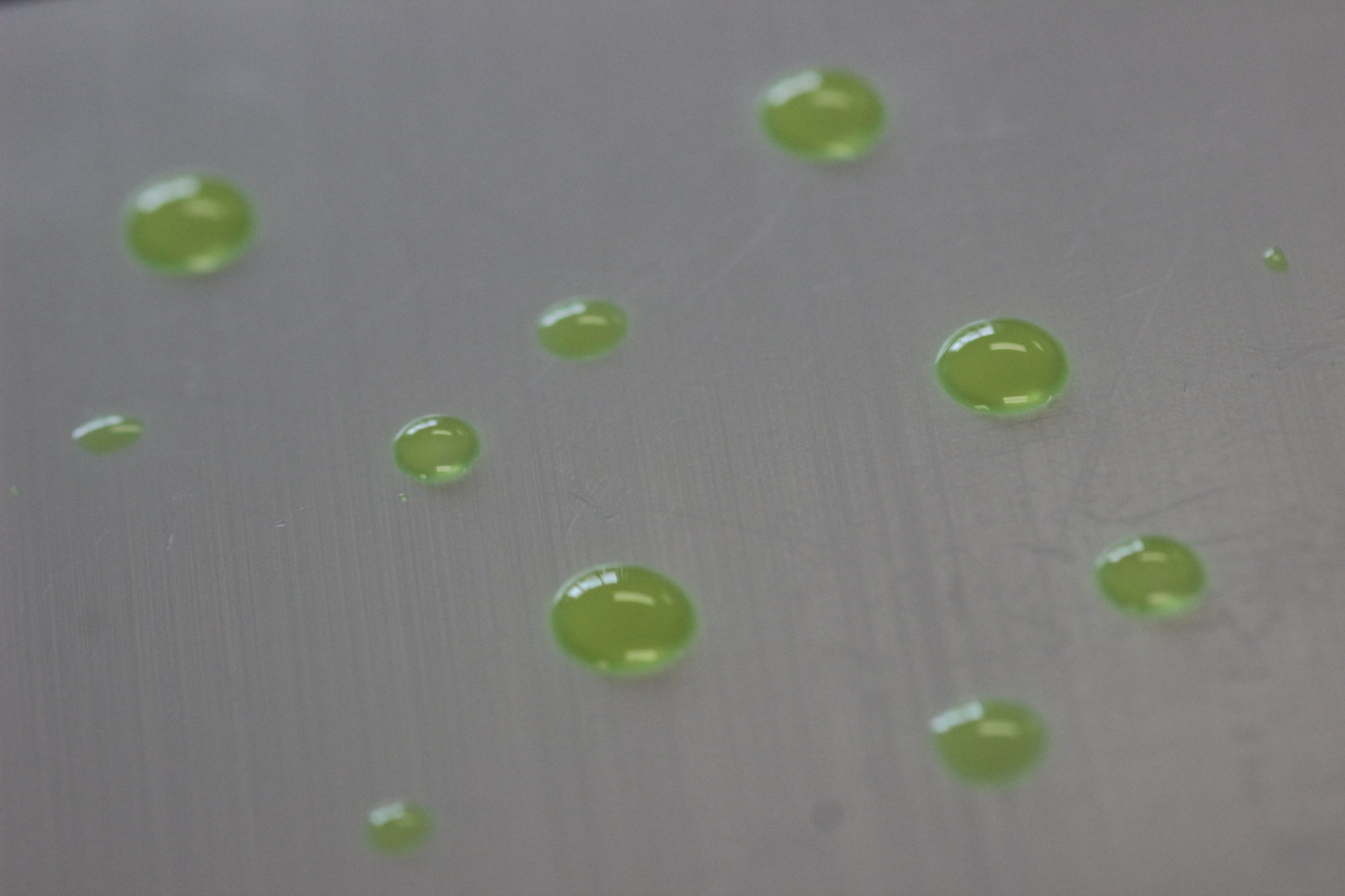
NanoSlic Coatings
NanoSlic coatings are both hydrophobic and oleophobic. With a water contact angle in the 105°-107° range and n-hexadecane contact angle in the 65°-70° range, these coatings provide a functional surface similar to PTFE. This high degree of water and oil repellency develops during the curing phase. As the solvent dries, highly non-polar molecules align themselves and form the coating’s surface. Below this layer, the bulk of the coating polymerizes into an inert silica-based structure. At the substrate surface, the polymer chemically bonds to hydroxyl groups on the substrate.
The advantage of this approach is that a high degree of hydrophobicity, oleophobicity, adhesion, temperature and abrasion resistance can be achieved as a one-step, low-cost process. NanoSlic can be applied by methods such as dipping and spraying and 3-dimensional surfaces can easily be coated. Very thin layers, in the 2-4 micron range provide excellent properties. Therefore, NanoSlic coatings are an excellent choice for the most demanding applications and challenging environments where hydrophobicity, oleophobicity and temperature resistance are required.