Ceramic Coatings
At its very basic level, a ceramic material is a solid material comprising an inorganic compound of metal, non-metal or metalloid atoms primarily held in ionic and covalent bonds. The crystallinity of ceramic materials ranges from highly oriented to semi-crystalline, vitrified, and often completely amorphous (e.g., glasses). Most often, fired ceramics are either vitrified or semi-vitrified as is the case with earthenware, stoneware, and porcelain. Varying crystallinity and electron composition in the ionic and covalent bonds cause most ceramic materials to be good thermal and electrical insulators (extensively researched in ceramic engineering). With such a large range of possible options for the composition/structure of a ceramic (e.g. nearly all of the elements, nearly all types of bonding, and all levels of crystallinity), the breadth of the subject is vast, and identifiable attributes (e.g. hardness, toughness, electrical conductivity, etc.) are difficult to specify for the group as a whole. General properties such as high melting temperature, high hardness, poor conductivity, high moduli of elasticity, chemical resistance and low ductility are the norm. (Wikipedia)
The Earliest Ceramics
The earliest ceramics were made of clay, either used by itself or mixed with other materials like silica and then hardened or sintered, by fire. Later ceramics were glazed and fired to create smooth, colored surfaces, with decreasing porosity through the use of amorphous ceramic coatings on top of the crystalline ceramic substrates.
Today’s Advanced Ceramics
In the 20th century, new ceramic materials were developed for use in advanced engineering applications, such as semiconductors. These materials often referred to as, “advanced ceramics,” can be composed of silicon carbide, tungsten carbide, chrome oxide, titanium dioxide, alumina-titania oxide, alumina oxide, zirconium oxide, magnesium zirconium oxide and others.
Typically, these advanced ceramic materials require specialized application methods for deposition such as; oxygen acetylene powder deposition, detonation guns, plasma spray, and chemical vapor deposition.
Therefore these ceramics are suitable for a limited range of applications, although some lower grade ceramic coating find use on such surfaces as pots and pans. These coatings do provide high-temperature performance but do not attain the properties of “advanced ceramics.”
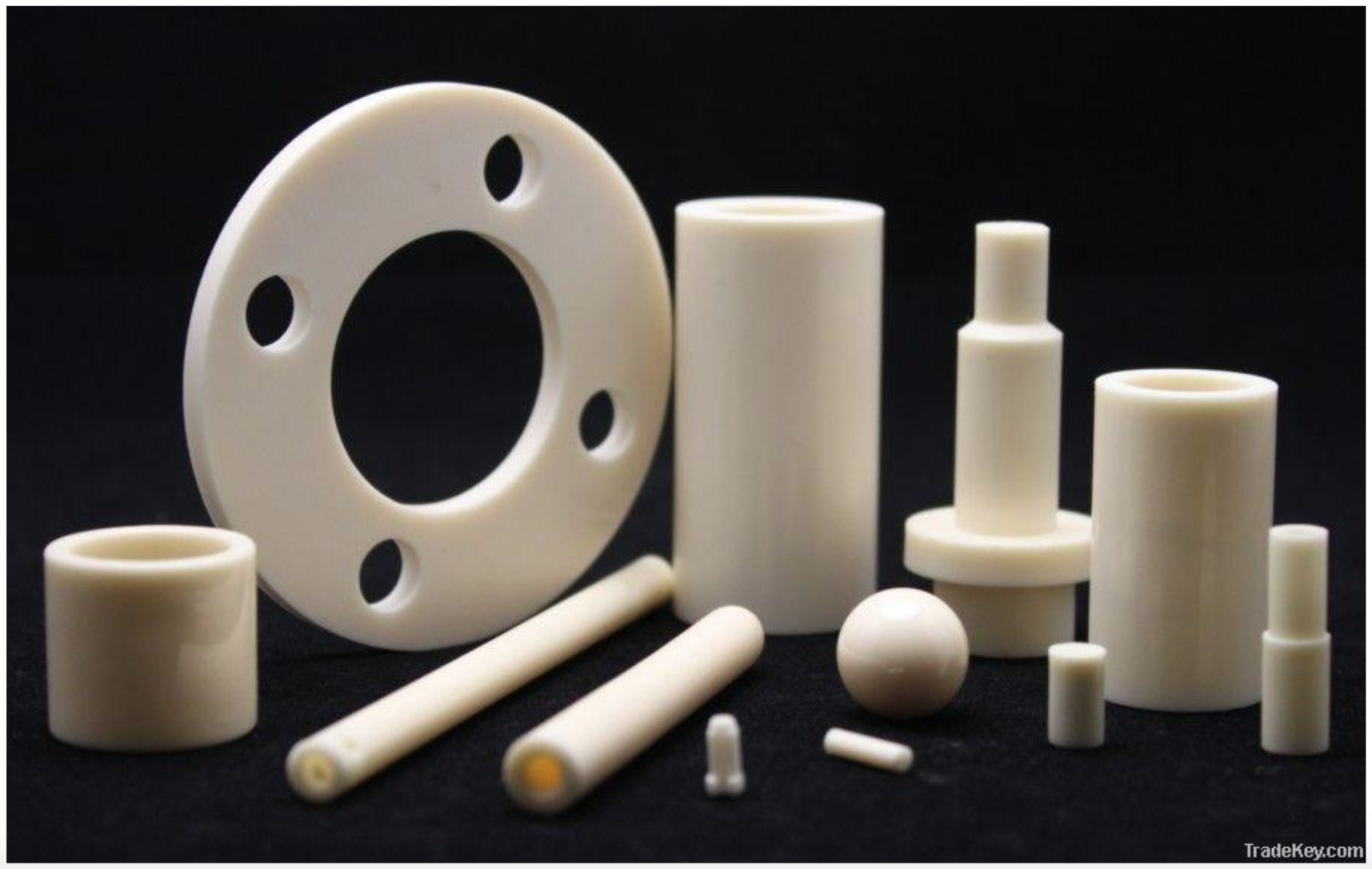
Still, these consumer grade ceramic coatings require specialized equipment for application and “firing.”
When you get beyond “old time” ceramics of clay and the “advanced ceramics,” definitions get really confusing. Some manufacturers offer products called ceramic coatings but are actually ceramic particles, in the form of powders or spheres, that are incorporated into a non-ceramic polymer binder. With such a binder, the coating can be applied by traditional methods such as spraying, wiping, and dipping. Coatings can be air or oven cured. The ceramic “filler” offers physical and chemical improvements to the coating, perhaps substantially but it is hard to say it is a true ceramic coating.
The non-ceramic polymer, primarily comprised of C-C bonds, does not have the temperature performance of a true ceramic. Some of these types of coatings may even use nanoscale (<100 nanometers) ceramic particles and then call the material a nano-ceramic coating.
How Does Nanoslic Work
NanoSlic coatings use a primary binder polymer that is ceramic, meaning its primarily composed of an inorganic material. On a weigh basis NanoSlic Coatings are largely composed of silica. Other materials are added for specific formulations and applications.
NanoSlic materials are inherently capable of maintaining properties at temperatures well beyond non-ceramic polymers.
NanoSlic is a revolutionary coating technology that offers many of the benefits of “advanced ceramics” but does not require a high cost, multi-step process that includes “firing.”
The product can be applied to a wide variety of surfaces. The required thickness of the coating will depend on the application and the desired result. Generally, the coating thickness with 1 – 4 microns. Traditional coatings are typically applied 50 microns or greater.
NanoSlic coatings are resistant to most solvents and are unaffected by a wide range of pH. Most formulations achieve 9H hardness.
By incorporating specific functional groups into the polymer, various properties can be achieved including:
- Hydrophobicity
- Oleophobicity
- Ambient temperature curing
- Heat-induced crosslinking
- Flexibility
- Outdoor weathering
- Conductivity
- Improved temperature resistance
- Reduced coefficient of friction